Real Time Error Numbers
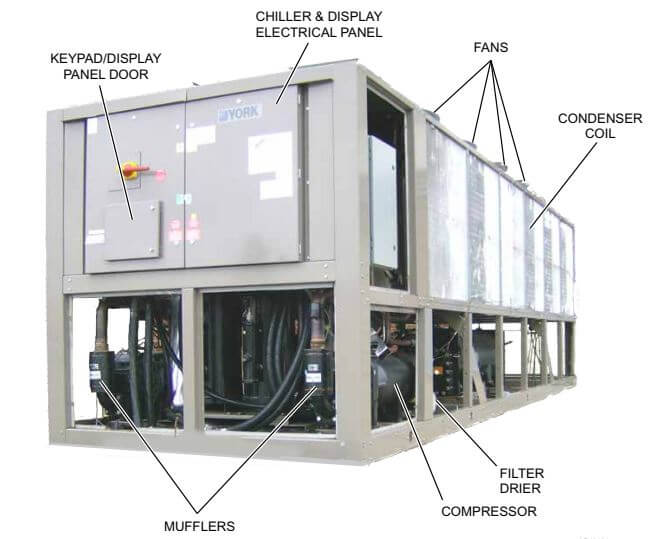
Error | Description |
---|---|
0 | All Ok |
1 | Datum Type Ok Test Failed |
2 | English Text Too Long |
3 | Floating Point Exception |
4 | Get Packet Failed |
5 | Get Type Failed |
6 | Invalid Unit Conversion |
7 | Invalid Hardware Selection |
8 | Real Time Fault |
9 | Spanish Text Too Long |
10 | Thread Exited |
11 | Thread Failed |
12 | Thread Stalled |
13 | Io Board Reset |
14 | Bram Invalid |
15 | Bacnet Setup Failed |
Problem: No display on panel – unit will not start
Possible Cause:
- Main supply to control system OFF.
- Emergency stop device off.
- CB3 tripped.
- No supply to – T2
- No 24VAC supply to power board.
- No +12V output from powerboard.
Action:
- Switch on main supply if safe to do so.
- Check if control panel emergency stop switch and any remote emergency stop devices are in the OFF position. Turn to ON position (1) if safe to do so.
- Check CB3
- Check 115VAC to L & 2.
- Check wiring from – T2 to powerboard and fuse.
- Replace powerboard or isolate excessive load on the board.
Problem: NO RUN PERM displayed (No run permissive)
Possible Cause:
- No liquid fl ow through the evaporator
- Flow switch or cycling contacts are not made
Action:
- Ensure that liquid pumps are running. Valves are correctly set and fl ow is established.
- Check that the fl ow switch is functional and is installed according to the manufacturer’s instructions. Check cycling contacts.
Problem: SYS # HIGH OIL TEMP
Possible Cause:
- Poor airfl ow through the condenser coils
- Measured temperature incorrect
Action:
- Check for airfl ow restrictions caused by blockages on intake faces of air coils.
- Check oil temp sensor and wiring.
Problem: Chiller FAULT: LOW AMBIENT TEMP displayed
Possible Cause:
- Ambient air temperature is lower than the programmed operating limit.
- Ambient air temperature is lower than the programmed operating limit.
- Measured temperature is incorrect.
Action:
- Use the ‘ambient temp.’ key to display the temperature and confi rm that the displayed value is approximately correct. The warning message should clear when the ambient air temperature rises above the programmed operating limit
- Check the programmed settings are correct for the options fi tted to the unit
- Check ambient sensor and wiring
Problem: Chiller FAULT: HIGH AMBIENT TEMP displayed
Possible Cause:
- Ambient air temperature is higher than the programmed operating limit.
- Ambient air temperature is higher than the programmed operating limit.
- Recirculated air is affecting the sensor
- Measured temperature is incorrect
Action:
- Use the ‘ambient temp.’ key to display the temperature and confi rm that the displayed value is approximately correct. The warning message should clear when the ambient air temperature falls below the programmed operating limit.
- Check that the programmed settings are correct for the options fi tted to the unit.
- Check fans are operating correctly and the rotation is correct. Check for airfl ow recirculation.
- Check ambient sensor and wiring.
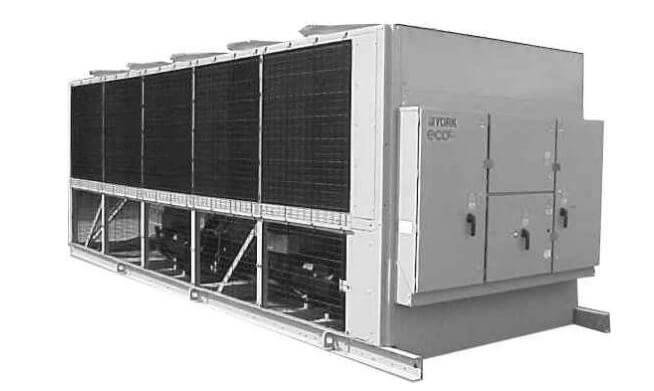
Problem: Chiller FAULT: LOW WATER TEMP displayed
Possible Cause:
- Leaving liquid drops below the programmed low limit faster than the unit can unload.
- Unit is not unloading.
- Measured temperature is incorrect.
Action:
- Check for restrictions in the liquid fl ow line. Check that the liquid fl ow is stable.
- Check the voltage to the unloader valve solenoid. Check that the compressor unloads correctly.
- Check water temp sensor and wiring.
Problem: Chiller FAULT: VAC UNDERVOLTAGE displayed.
Possible Cause:
- Poor main supply voltage.
Action:
- Check main supply is stable and within allowable limits.
- Check for voltage dip on compressor start.
Problem: SYS # HIGH DSCH displayed (High discharge pressure trip)
Possible Cause:
- Poor airfl ow through condenser coils.
- Excessive refrigerant charge.
- Measured pressure is incorrect.
Action:
- Check for airfl ow restrictions caused by blockages on intake faces of air coils. Check for damaged fi ns/return bends. Check for correct fan operation and direction of rotation. Check for non-condensables (air) in system.
- Check that the sub-cooling is correct.
- Check discharge transducer and wiring.
Problem: SYS # HIGH DSCH TEMP displayed (High discharge temperature)
Possible Cause:
- Suction superheat too high.
- Poor airfl ow through the condenser coils.
- Measured temperature incorrect.
Action:
- Check suction superheat is within range.
- Check for airfl ow restrictions caused by blockages on intake faces of air coils.
- Check discharge sensor calibration, location and wiring.
Problem: SYS # DSCH LIMITING displayed (Discharge pressure unloading)
Possible Cause: Discharge pressure unloading due to unit operating above load limit. See also SYS # HIGH DSCH.
Action: Check chilled liquid temperature is within range. Check fan operation. Check if ambient air temperature is above design conditions. Check programmed unload point.
Problem: SYS # HIGH OIL PRESS DIFF is displyed. (High oil differential pressure.)
Possible Cause:
- Ball valve in oil circuit closed.
- Dirty / blocked oil fi lter
Action:
- Check ball valves are open position.
- Check and change oil fi lter cartridge.
Problem: SYS # LOW SUCTION displayed
Possible Cause:
- Badly adjusted or faulty expansion valve.
- Reduced evaporator performance.
- Low refrigerant charge.
- Restricted refrigerant flow.
- Measured pressure incorrect.
Action:
- Check superheat.
- Check for restricted chilled liquid flow. Check for fouled tube surfaces. Check superheat.
- Check subcooling is correct. Check for leaks.
- Check for blocked fi lter / drier. Check LLSV is opening correctly.
- Check suction pressure transducer and wiring.
Problem: SYS # LOW CURR/MP/HP displayed
Possible Cause:
- Compressor current too low.
- Measured current is incorrect.
- Compressor motor protector signal failure.
- Mechanical high pressure cut-out trip.
- No motor cooling.
Action:
- Check the compressor main supply voltage, fuses, contactors and wiring. Check main supply voltage is within tolerance. Check 2ACE MP fault code.
- Check for defective Motor Protector Module.
- Check motor protector and wiring.
- Check compressor discharge valve is open. Check cut-out and wiring.
- Check superheat. Check operation of economizer, TXV, and liquid solenoid valve.
Problem: SYS # CURR LIMITING displayed (Compressor current unloading.)
Possible Cause: High compressor motor current has activated unloading.
Action: Check if liquid temperature is within operating limits. Check if ambient air temperature is above operating limits.
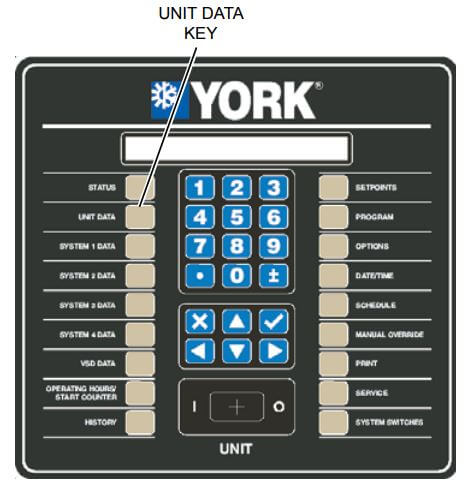
Comments